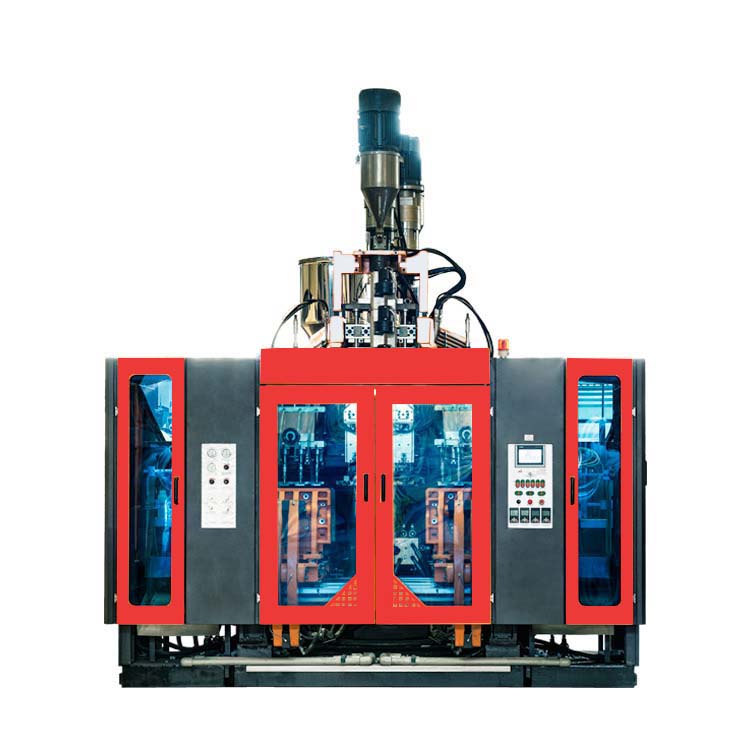
Blow Moulding adalah proses penting dalam pembuatan produk plastik berongga, dari botol hingga wadah besar. Faktor kunci yang mempengaruhi efisiensi dan kualitas proses ini adalah waktu pendinginan. Mengoptimalkan waktu pendinginan tidak hanya meningkatkan efisiensi produksi tetapi juga memastikan integritas dan kekuatan produk akhir. Di sini, kami mengeksplorasi teknik manufaktur canggih, desain sistem pendingin inovatif, kontrol suhu yang tepat, dan layanan OEM/ODM yang komprehensif yang dapat secara signifikan mengoptimalkan waktu pendinginan dalam mesin cetakan blow ekstrusi.
Teknik manufaktur canggih
Salah satu strategi terkemuka untuk mengoptimalkan waktu pendinginan adalah adopsi teknik manufaktur canggih. Teknik-teknik ini termasuk penggunaan mesin cetakan pukulan berkecepatan tinggi yang dilengkapi dengan kemampuan pendinginan yang ditingkatkan. Sekrup plastisisasi dan pencampuran efisiensi tinggi, bersama dengan mekanisme pembukaan dan penutupan cetakan presisi, sangat penting. Inovasi ini mengurangi waktu siklus dan meningkatkan kecepatan produksi secara keseluruhan. Selain itu, memanfaatkan cetakan multi-lapisan dapat meningkatkan sifat dan nilai produk, memastikan pendinginan yang seragam dan mengurangi risiko cacat.
Desain Sistem Pendingin Inovatif
Desain sistem pendingin yang inovatif memainkan peran penting dalam meminimalkan waktu pendinginan. Mesin cetakan blow modern dilengkapi dengan saluran pendingin dan sistem canggih yang memungkinkan disipasi panas yang cepat. Sistem pendingin air, dioptimalkan dengan saluran yang ditempatkan secara strategis di dalam cetakan, memastikan pendinginan yang merata dan efisien. Selain itu, mengintegrasikan sistem pendingin berbantuan udara dapat lebih jauh mengurangi waktu pendinginan dengan memberikan pendinginan langsung dan seragam ke bagian yang dicetak. Sistem ini dirancang agar hemat energi, sehingga mengurangi biaya operasional sambil meningkatkan kinerja pendinginan.
Kontrol suhu yang tepat
Kontrol suhu yang tepat sangat penting untuk mengoptimalkan waktu pendinginan dalam proses cetakan pukulan. Menerapkan sistem kontrol suhu yang canggih memastikan bahwa suhu cetakan secara konsisten dipertahankan pada tingkat yang optimal. Ini dapat dicapai melalui penggunaan sistem kontrol suhu loop tertutup yang terus memantau dan menyesuaikan proses pendinginan secara real-time. Kontrol suhu yang akurat mencegah overheating dan undercooling, yang keduanya dapat menyebabkan cacat produk dan peningkatan waktu siklus. Unit kontrol suhu tingkat lanjut mampu mengelola beberapa zona dalam cetakan, memberikan pendinginan yang tepat dan individual sesuai kebutuhan.
Layanan OEM/ODM yang komprehensif
Memanfaatkan OEM komprehensif (produsen peralatan asli) dan layanan ODM (produsen desain asli) dapat secara signifikan memengaruhi optimalisasi waktu pendinginan. Layanan OEM/ODM menawarkan solusi khusus yang disesuaikan dengan persyaratan produksi tertentu. Dengan bekerja sama dengan produsen, layanan ini memastikan bahwa mesin cetakan pukulan dirancang dan dikonfigurasi untuk memenuhi kebutuhan pendinginan yang tepat. Kustomisasi ini mencakup merancang sekrup dan batang inti yang berbeda untuk berbagai karakteristik plastik, memfasilitasi bahan yang mudah dan pergantian warna, dan memastikan bahkan distribusi ketebalan dinding. Selain itu, layanan komprehensif sering kali mencakup pengembangan desain cetakan khusus yang menggabungkan teknologi pendinginan canggih, lebih meningkatkan efisiensi.
Kesimpulan
Mengoptimalkan waktu pendinginan dalam mesin cetakan blow adalah pendekatan beragam yang melibatkan teknik manufaktur canggih, desain sistem pendingin yang inovatif, kontrol suhu yang tepat, dan layanan OEM/ODM yang komprehensif. Dengan mengintegrasikan strategi ini, produsen dapat mencapai siklus produksi yang lebih cepat, pengurangan biaya operasional, dan produk berkualitas lebih tinggi. Evolusi berkelanjutan dari teknologi blow cetakan menjanjikan efisiensi dan inovasi yang lebih besar di masa depan, mendorong industri menuju proses manufaktur yang lebih berkelanjutan dan hemat biaya.